江苏神马电力股份有限公司
基于质量溯源的复合绝缘子智能工厂采用全流程数字化集成架构,以先进工业网络应用与BI数据平台应用及分析为中枢,形成“设计、生产、供应链、质量”四层集成架构,为行业提供了可复制的数字化转型样板,构建了电力绝缘子行业技术制高点,推动我国输配电装备制造向高端化、绿色化、智能化跃升,具备显著的产业引领价值。
(一)政策需求
我国实施的制造强国战略,将智能制造作为主攻方向,并发布了《智能制造发展规划》《“十四五”智能制造发展规划》推动智能制造发展。江苏省制定了《江苏省“十四五”制造业高质量发展规划》《江苏省制造业智能化改造和数字化转型三年行动计划(2022-2024年)》《江苏省智能制造示范工厂建设标准》等文件推动落实制造强国强省战略。
(二)市场推动
“双碳”战略目标引领全球绿色电能快速发展,能源转型加大了全球电网投资,发达国家老旧电网的升级改造、发展中国家的电网基础设施的持续投入,带来全球对高质量电力设备需求的迅速增加。
江苏神马电力股份有限公司作为全球领先的电力系统外绝缘研制高新技术企业,需通过智能制造实现更快的响应速度、更高的资源利用率、更强的市场竞争力来抢占技术制高点,进一步巩固行业龙头地位。
以智能制造场景为载体,深度融合信息技术与电力装备制造工艺,构建覆盖研发、生产、供应链、质量管理的全流程数字化体系,并形成数字化工厂架构创新、智能制造技术突破、质量管控体系升级等多项行业领先技术突破。采用全流程数字化集成架构,以先进工业网络应用与BI数据平台应用及分析为中枢,形成“设计-生产-供应链-质量”四层集成架构。集成MES、ERP及工业互联网平台,实现全流程数据贯通。
核心实施场景
图1 仿真设计与验证
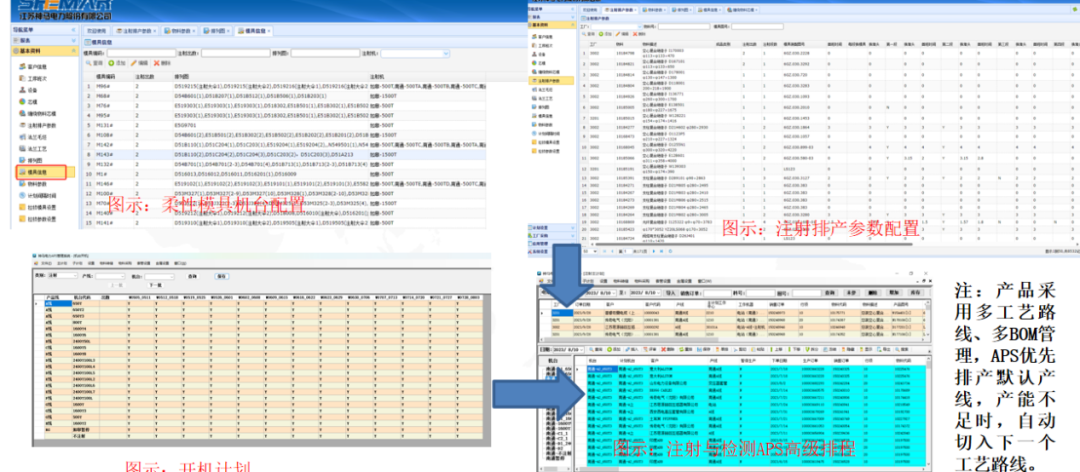
图2 智能排产
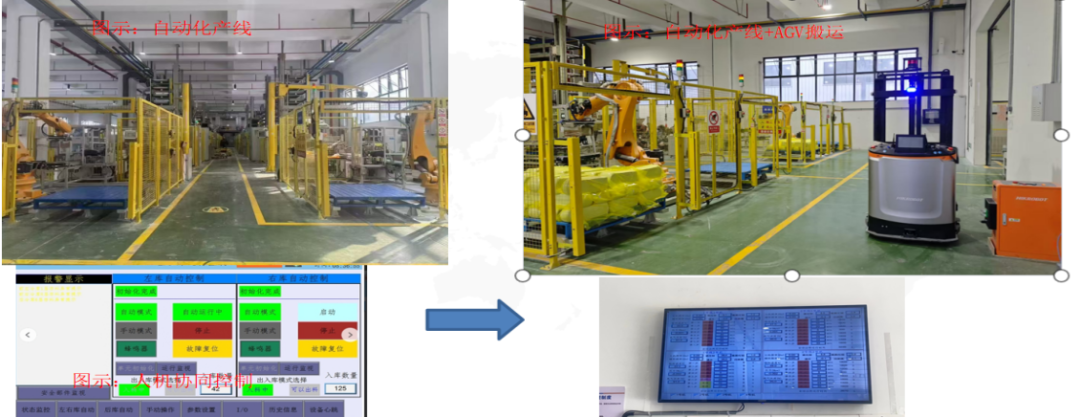
图3 人机协同
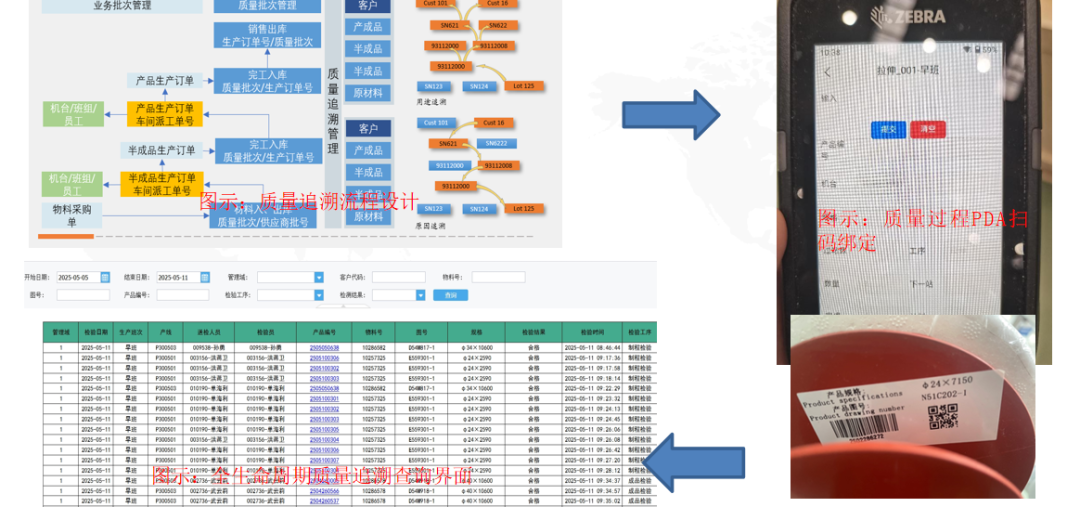
图4 质量溯源
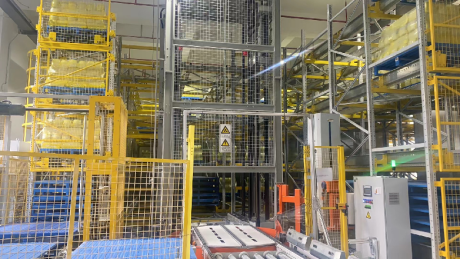
图5 物流配送
(一)总周期与投资
周期:2021年1月-2023年12月(3年),分设计、实施、优化三阶段;
总投资:2.3亿元。
(二)分项投入
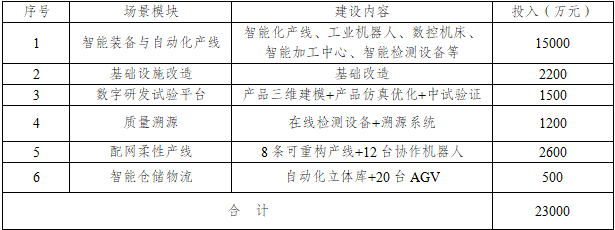
(一)量化成效对比
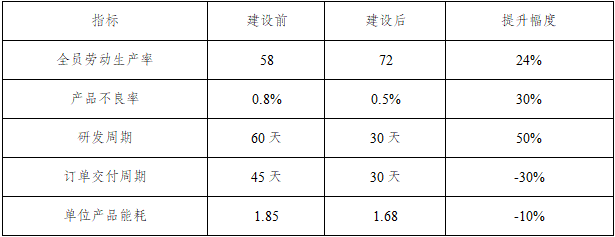
(二)标杆示范亮点
(1)复合绝缘子参数化建模:数据驱动模型下的输配电绝缘子产品快速研发;
(2)智能排程和生产柔性能力:多产线多产品快速切换;
(3)国家5G工厂:实时监测与精准追溯,实现绝缘子“一码溯源”;
(4)绿色制造:光伏+余热回收覆盖56%能源需求。
(一)成功经验
(1)智能排程方法论创新:首次使用同一物料多工艺、多BOM排程规则,按照默认产线工艺优先,产线产能不足,自动切入第二工艺、第三工艺,根据工艺的不同,选择不同的制造BOM版本,实现柔性高级排程;
(2)参数建模驱动产品快速设计:借助三维设计软件和参数数据库,开发产品设计向导,缩短产品设计周期,快速市场反应,大模型库支持由传统研发向AI转型;
(3)数据资产化:沉淀大量销售、研发、工艺、质量数据,支撑AI模型可持续优化。
(二)教训与改进
初期规划不足。首期电网复合绝缘子自动化产线设计工艺参数考虑不完整,导致参数调整后自动化产线停用。重新调整和优化产线程序,适应性提升90%。
(三)待优化方向
扩大供应商协同平台的推广使用,逐步实现供应商数智化管理。
南瑞继保:打造电力装备行业智能工厂标杆
在电力装备行业智能化转型的浪潮中,南京南瑞继保以“柔性制造+自主创新”双轮驱动战略,成功打造了一座覆盖研发、生产、运营全流程的智能工厂,不仅实现了自身效率与质量的全面提升,更成为行业数字化转型的典范。在这里,电力装备的未来,正被重新定义。
效率革命:从“月”到“天”的跨越
智能工厂的建成,让南瑞继保的生产效率实现质的飞跃。通过柔性制造体系的构建,企业生产周期大幅缩短,订单交付时间从1个月压缩至10天。更令人瞩目的成就是:在员工规模稳定的情况下,企业年产量实现翻倍增长,创造了“人效双升”的制造奇迹。
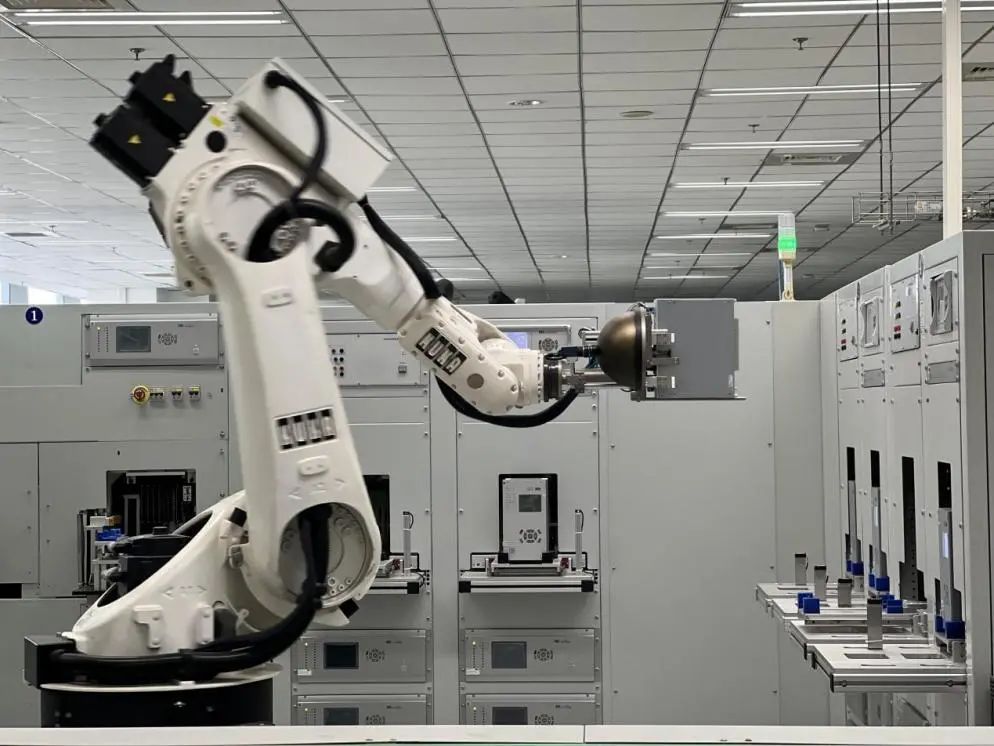
装置智能测试系统
质量跃迁:从“优良”到“卓越”的蜕变
智能化改造为产品质量装上“智慧引擎”。通过全流程智能检测与自动化升级,产品直通率逼近100%。这不仅为电力系统的安全运行提供了更高保障,更让南瑞继保赢得国内外市场的广泛认可。
行业赋能:从“标杆”到“灯塔”的突破
南瑞继保深度总结智能工厂建设经验,构建起贯穿研发设计、柔性制造、智慧运营的全链条转型体系。这套涵盖数字化协同、智能生产、资源优化的解决方案,不仅推动企业自身升级,更为行业上下游提供了从技术创新到管理变革的完整方法论,成为离散制造领域智能化转型的“实践指南”。